Refining and processing
Based on the experience gained and in order to satisfy the market demand, we also deal with the refining and transformation of numerous zinc-based materials in primary zamak ingots in compliance with UNI EN 1774 standards. This service has been a remarkable commercial success, offering a real exchange of goods between our Company and the die casting companies.
The logic behind this method is that the die casting companies supply several types of materials with a high zinc content to the production process developed by S. Erasmo Zinkal; these materials are carefully selected, refined through melting and then converted into zamak alloy ingots.
The advantages of the above-mentioned process are remarkable, specifically:
- Recovery of materials otherwise not usable.
- Elimination of remelting processes within the die casting companies, with remarkable savings in terms of dedicated personnel, electric energy and gas consumption, and maintenance.
- The die casting companies are certain that their product complies with the provisions of the European standard UNI EN 1774: the melting process provides for appropriate additions of aluminium, magnesium and copper in order to obtain ingots compliant with the above-mentioned standard.
- Lower expenditure and financial exposure.
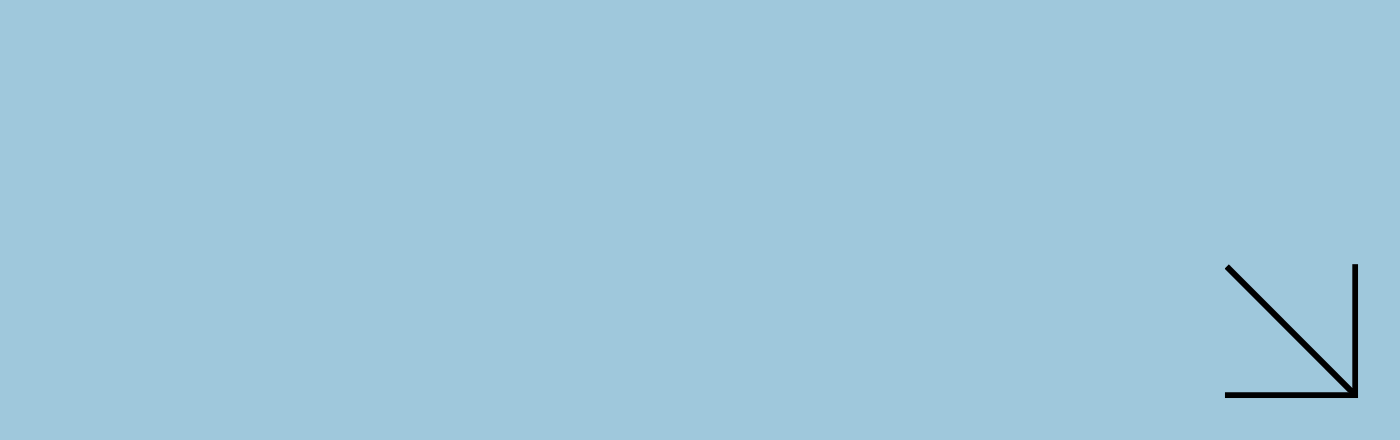
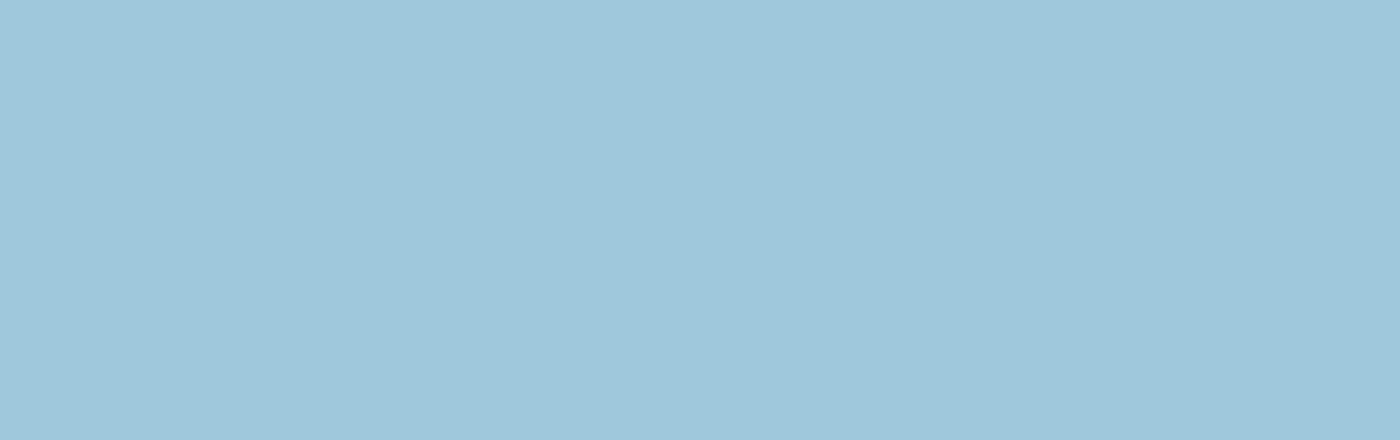
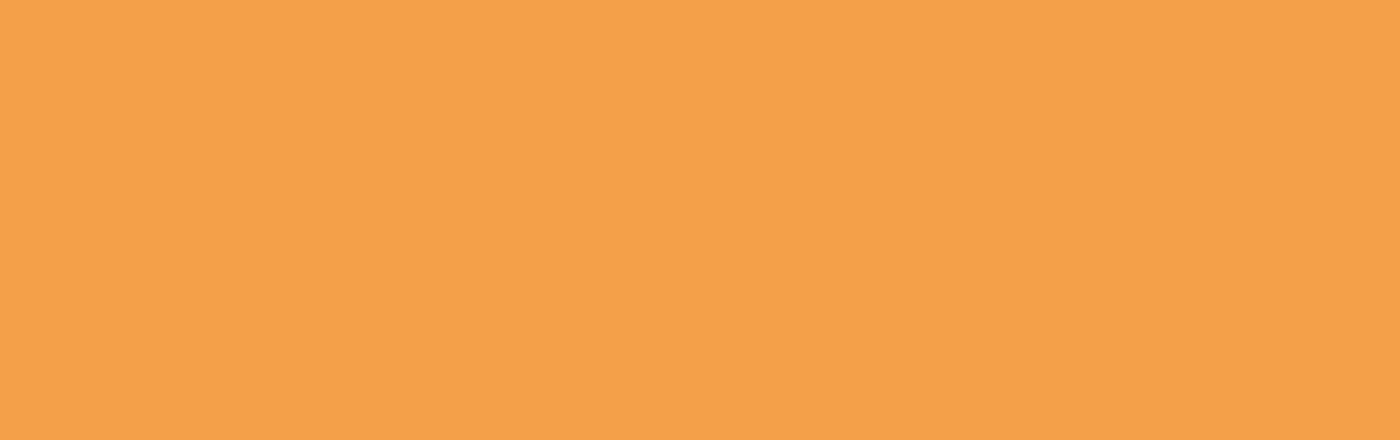
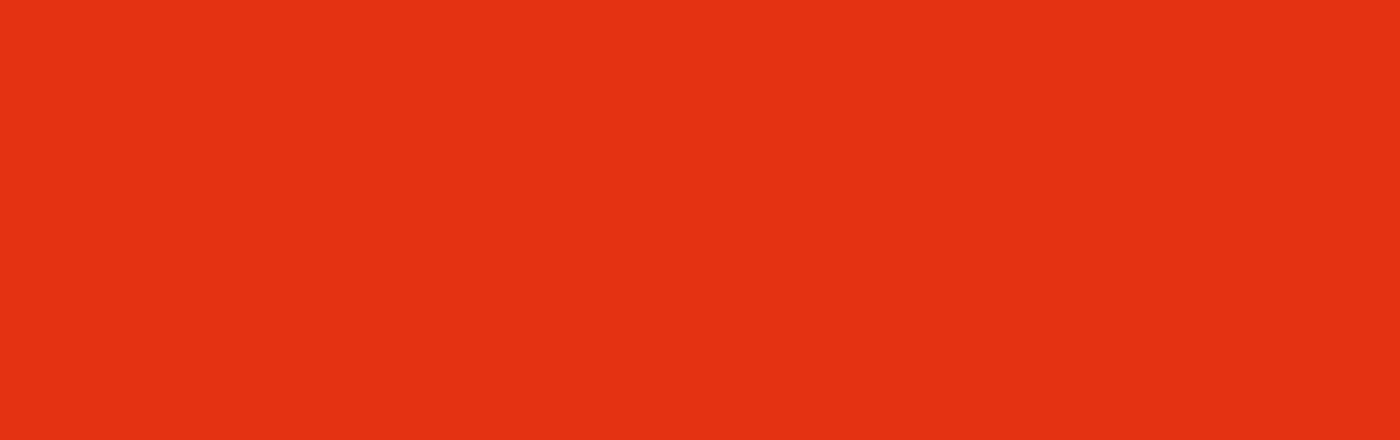
Our range of products
As mentioned above, our Company produces different types of zamak alloy, all of which contain a high percentage of hyper-pure SHG zinc (99.995% purity), with varying proportions of aluminium, magnesium and copper, added to the melting furnace in predetermined percentages according to the specific demands of our customers.
Zamak 15 is the most popular alloy both in the domestic market and the international markets, followed by Zamak 12, Zamak 13 and Zamaksave, with similar sales percentages; Zamak Kayem, designed for very sophisticated uses, has a lower demand rate.
Circular economy
Our zinc alloys also originate from the massive use of production scrap and by-products that we purchase, a method that meets circular economy criteria; we convert the commodities defined as “waste” by the standards into a finished product, thus avoiding onerous and harmful landfill sorting.